
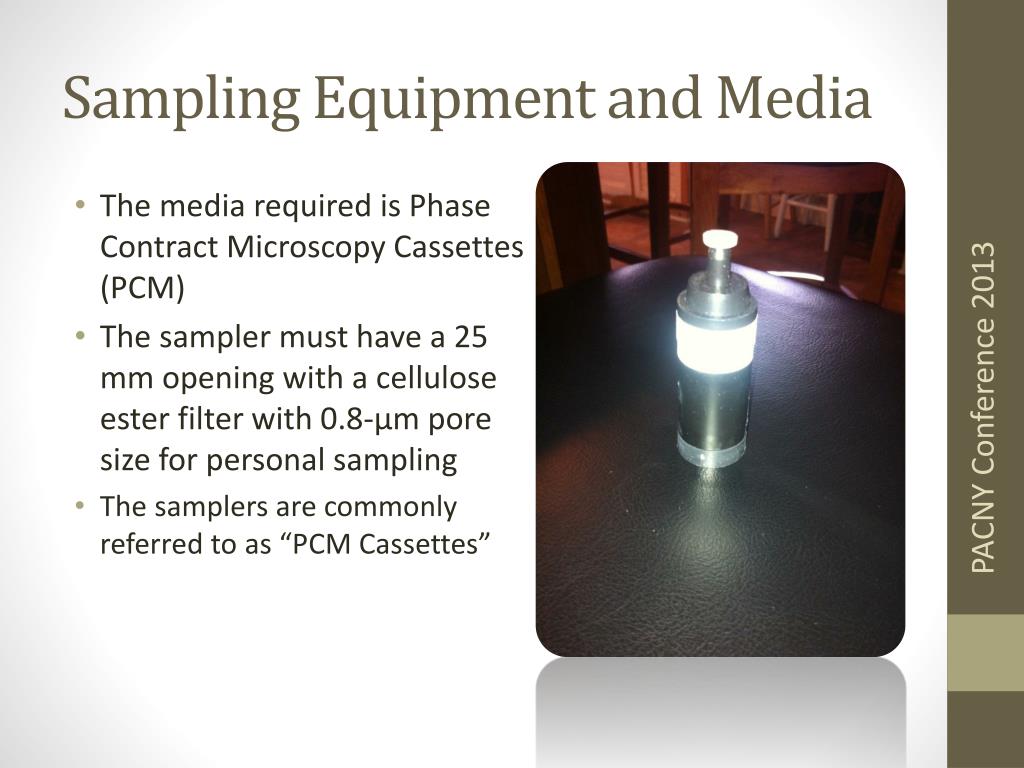
This would create an artificially low concentration.
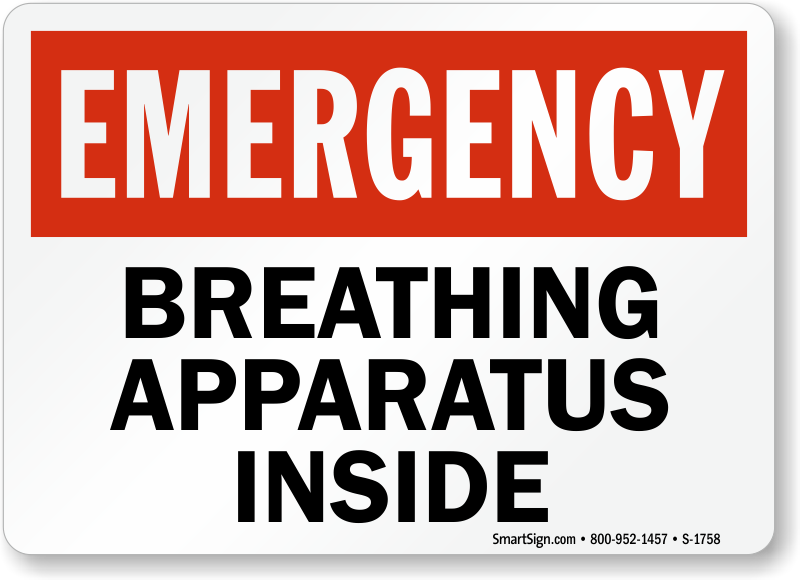
It also would be measuring an unrepresentative atmosphere composed of a mixture of the air passing out of the respirator and the air outside the hood. Sampling inside the hood would indeed eliminate the abrasive particles being driven into the cassette by the force of the blasting operation. Since we are concerned with what an employee's potential exposure would be, it must also be located outside of any protective equipment. It should be as close as possible to the nose and mouth of the employee, i.e., in a hemisphere forward of the shoulders with a radius of 6 to 9 inches. The correct placement for air sampling cassettes is near the breathing zone of the employee. Your letter then offers several arguments why the cassette should be inside the hood. In your letter you have ask for an official statement regarding the correct placement of the air sampling cassette on your abrasive blasters when testing the breathing zone concentrations of abrasive blast dust. Your letter has been forwarded to OSHA's National Office for response. Gabriel Gillotti, Director of the Occupational Safety and Health Administration's (OSHA's) San Francisco Regional Office, Office of Voluntary Programs and Outreach. The 30 second interval is adjustable.This is in response to your October 14, letter addressed to Mr. The 3 LED lights will continue to flash once every 30 seconds until the non-compliance condition has been resolved. The instrument flashes it’s 3 LED lights every 30 seconds in the following conditions if the instrument has not been bump tested, or if calibration is due, or if there was a gas alarm event.
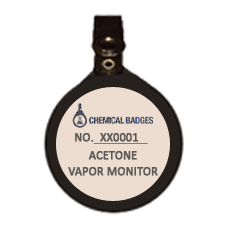
Safety supervisors will appreciate the non-compliance indicator. H2S and CO are now available in a combo micro sensor. The new O2 sensor is electrochemical with a 3 to 5 year life span. If one filament gets poisoned the second filament takes over. The LEL sensor has a unique design with two active filaments in one sensor to increase it’s resistance to silicone poisoning. The GX-3R represents the latest evolution of gas detection technology utilizing a new generation of micro sensors. It simultaneously monitors and displays LEL combustibles, O2, CO (Hydrogen compensated CO also available), and H2S.
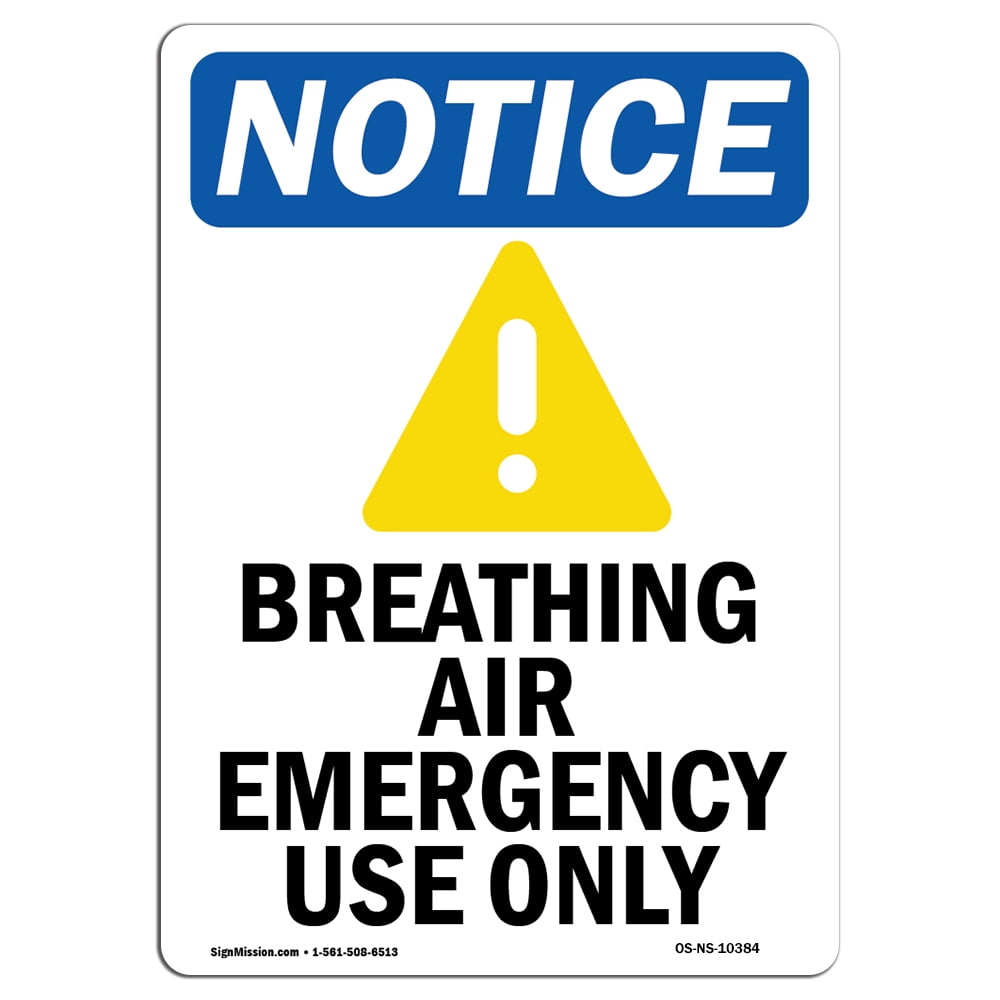
The GX-3R is the worlds smallest 4 gas monitor weighing only 3.52 ounces and can comfortably be clipped within a worker’s breathing zone (2.2” W x 2.55” H x 1.02” D). Now there is a 4 gas monitor smaller than many single gas monitors. Traditionally this means only a single gas monitor would be small enough for a worker to practically wear a gas monitor ‘In the breathing zone’. Air sampling filters may be attached to the collar or lapel. OSHA defines the breathing zone as a ten inch radius around the worker’s nose and mouth, and requires that worker exposure monitoring air samples be collected in the breathing zone.
